Cost of living pressures may be forcing ordinary Australians to watch their weekly living costs,…
Pathways to reduce dairy farm energy costs
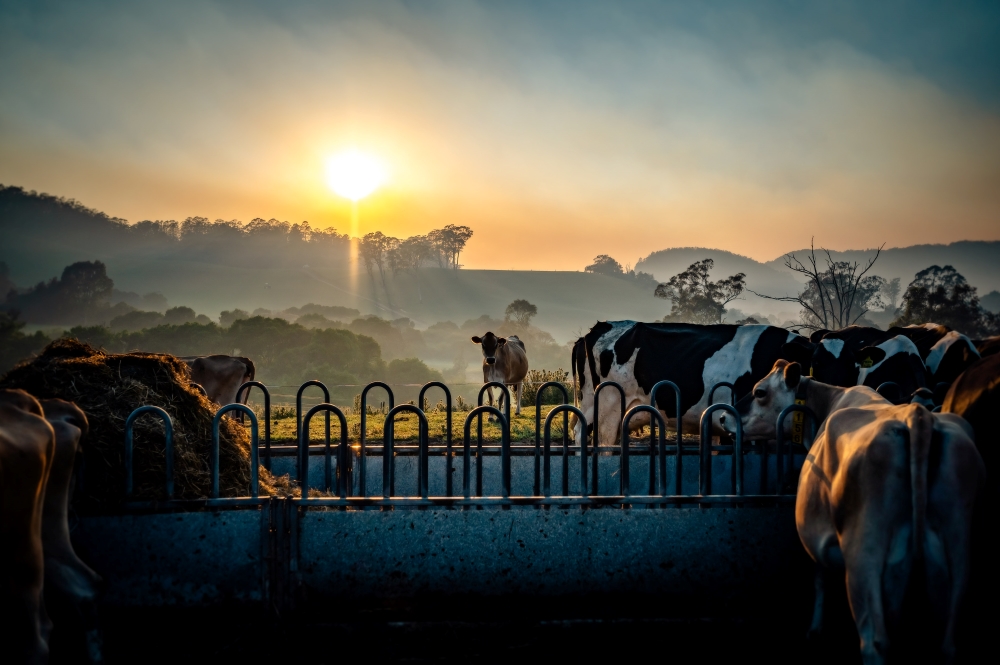
A NSW Farmers’ led research project has found there are energy savings to be made for dairy farmers in getting milk from the cow to filling the milk tanker for delivery.
This short but costly step in the dairy supply chain accounts for around 80 per cent of a dairy farm’s energy costs, mainly due to the need to cool and store large volumes of milk below 5.5°C. The cooling must also occur within a narrow window of time, resulting in high peak demand costs.
Running milking equipment and hot water systems also contribute to a heft electricity bill, which can be up to $80,000 annually for an average sized dairy farm.
Inspired by changes in Australia’s energy mix and significant electricity cost increases for dairy farming businesses, NSW Farmers and Norco teamed up to identify the least cost pathways to reducing on-farm energy costs like refrigeration.
The NSW Department of Primary Industries (DPI) funded the Agricultural Renewable Energy Acceleration (AREA) project, in collaboration with the University of Technology Sydney Institute of Sustainable Futures (UTS ISF), the University of NSW (UNSW) and Essential Energy.
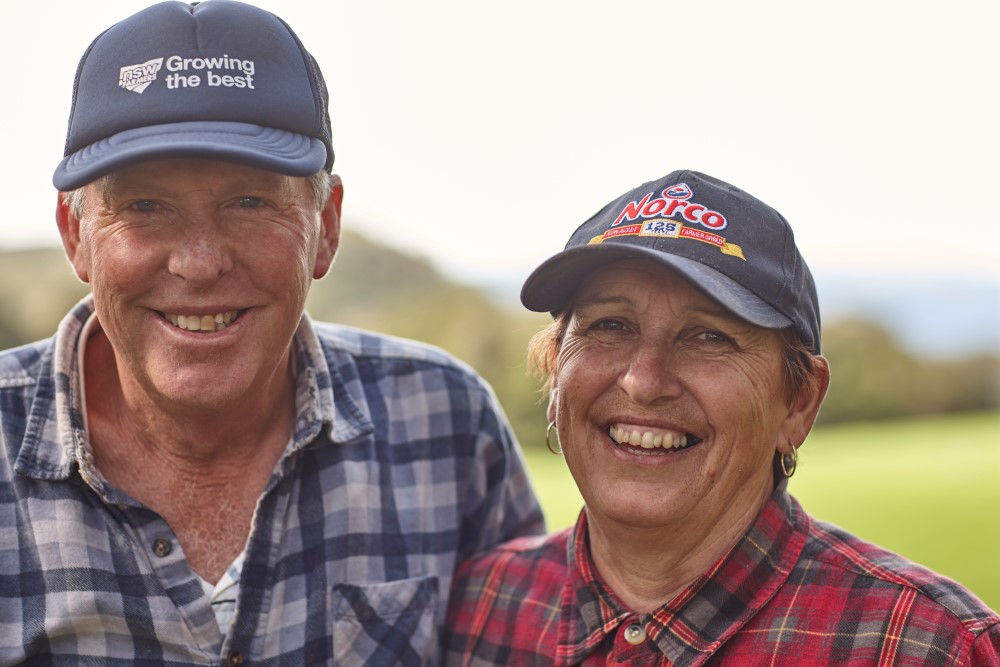
The project included an energy audit of ten dairy farms supplying Norco in the Northern Rivers and north coast regions, with the farm’s annual milk production ranging from 387,000 litres to 2.4 million litres.
Conducted by pitt & sherry consultants, the extensive review of the dairies milk processing, cooling equipment and hot water systems revealed an average energy use of 51.7 kWhr per 1000 litres of milk.
This compares to a national average energy use on dairy farms of 48 kWhr/kL of milk. (Source: Saving Energy on Dairy Farms report, Dairy Australia, 2018).
Energy use per kL milk was highly variable amongst the 10 dairies, ranging from 27 to 75 kWhr/kL. There was a herd size impact on energy use, with farmers with larger herd sizes having lower energy use per kL milk.
The energy audits recommended a typical order of upgrades for dairy farms that included milk pre-cooling, vacuum pump upgrades, refrigeration upgrades, heat recovery and hot water adjustments and metering and monitoring.
Using the farm energy audit data, the University of NSW tested how solar systems could offset dairies’ peaky energy demand. Some solar systems could reduce the daily farm energy bill by about 30-40%. Adding batteries could further reduce daily farm energy bills by 5–10% where battery decisions are optimised to minimise daily electricity use.
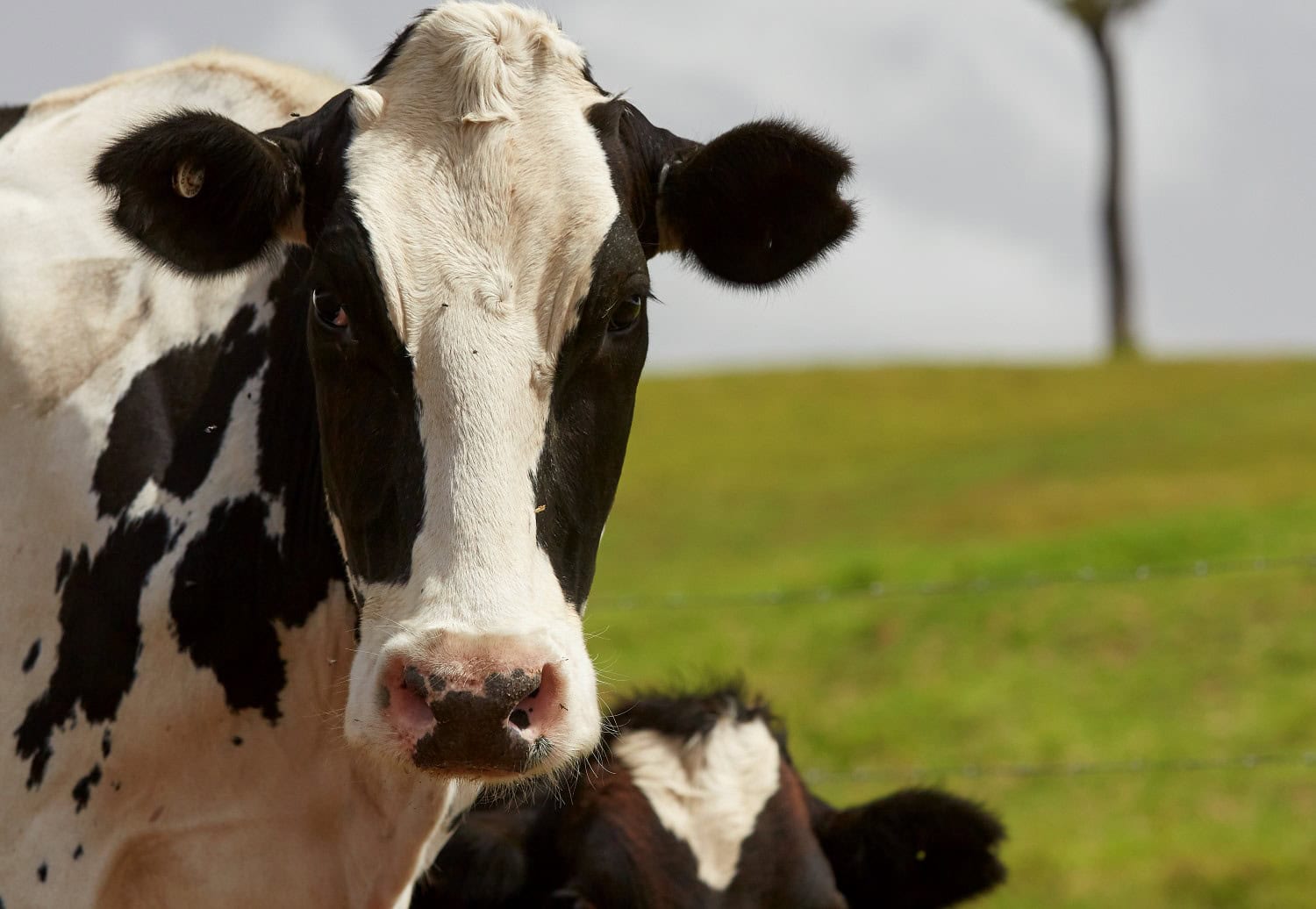
Cooling energy costs on the dairy farm
The 10 dairy audits demonstrated pre-cooling the milk before the entering vat can reduce overall refrigeration use by 25%.
Eight of 10 dairy farms have already adopted a pre-cooling step, which typically requires a water storage tank, plate cooler heat exchanger (HX) and a water pump to reduce the milk temperature from 37°C to 20°.
“The most immediate upgrade is to have milk pre-cooling as this predictably and reliably reduces the immediate energy demand and energy consumption of a dairy significantly,” said Christopher Horvath from pitt & sherry
Christopher said the audits found further ways maximise the effectiveness of this measure such as adjustments to pump speeds and volumes, achieving constant supply temperatures through milking and reviewing water tank location.
“Where already in place, measurements of water and milk temperatures before and after each milking and on different days, and volumes used can be reviewed to further improve energy savings.
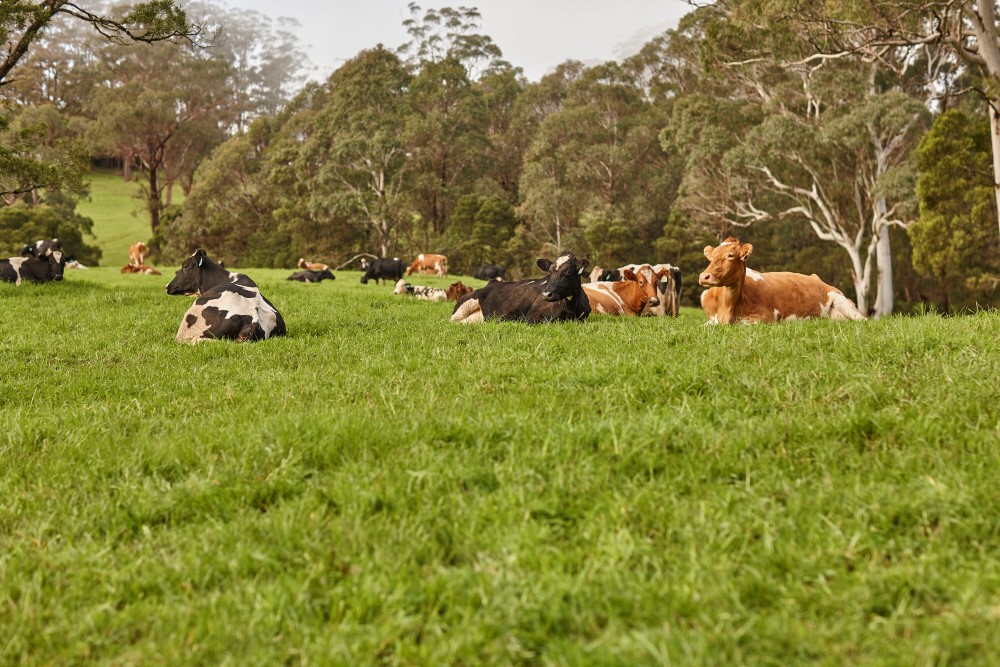
“Upgrading to new refrigeration technology also provided efficiency advancements, in addition to other benefits such as reduced maintenance, manual cleaning, and improved reliability.”
Upgrades for vacuum pumps used to for milking, heat recovery and water adjustments and installing metering equipment were identified as other steppingstones on the pathway to reducing energy costs.
Five of the dairy farms selected for metering with Wattwatchers to provide insights into capital investment costs and how many years it would take to pay it back. The estimated cost of upgrades ranged from $13,200 to $62,000 with payback periods from two to seven years.
As part of the project, NSW Farmers has produced an Energy Productivity Guide for Dairy Farms, two case studies examining Dairy Energy Efficiency Options, and a final report on the AREA Initiative. These can be found here.
The AREA Project was conducted as part of the NSW Primary Industries Climate Change Research Strategy funded by the NSW Climate Change Fund.
Dairy Australia has launched a new campaign to get people into the industry. Check it out here.