Farmers shook their heads with disbelief when panic buying gripped the country in March, with…
Post-harvest infrastructure special report
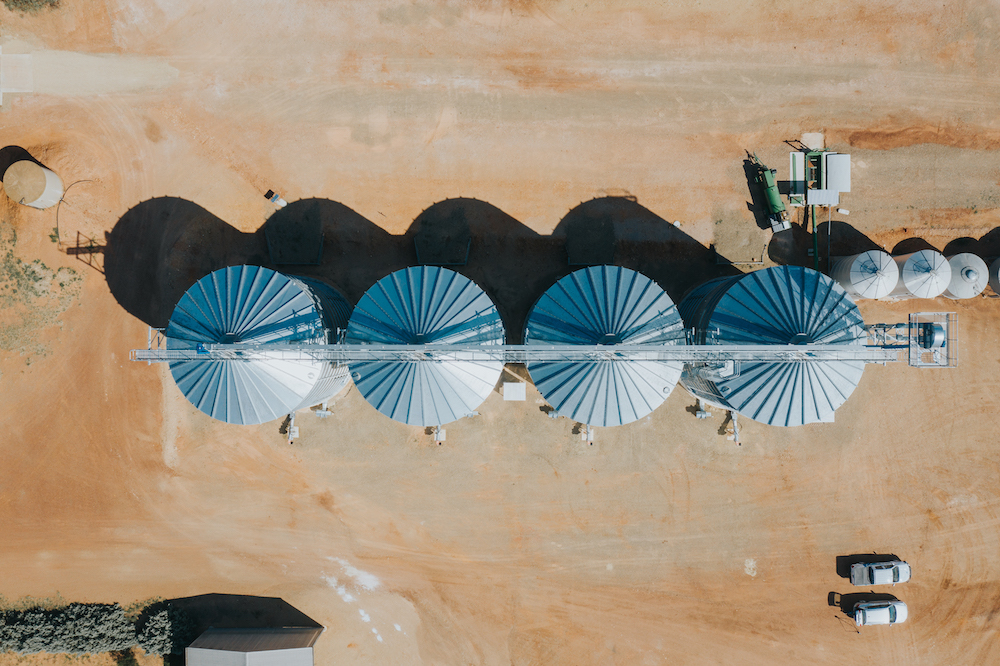
Three years of drought in Eastern Australia were followed by one of the best autumn breaks in years leading to forecasts of record grain harvest and a burst of optimism in the agricultural sector. For farm shed and silo manufacturers, this confidence coupled with the $150,000 instant asset write off brought down in the recent federal budget has boosted demand for post-harvest infrastructure.
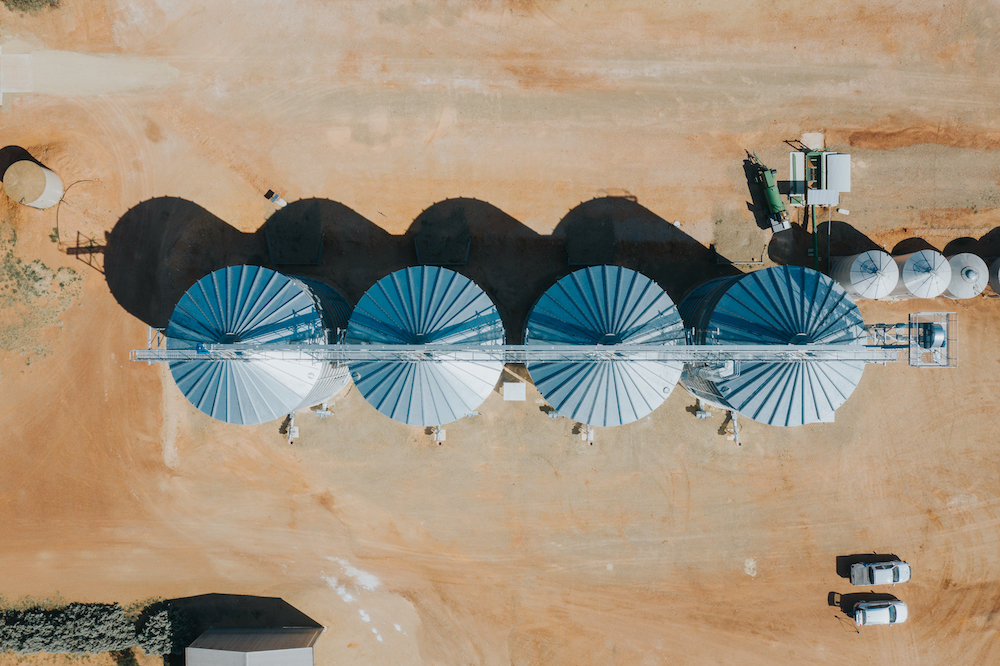
At the same time, a shift to putting solar panels on the roofs of farm buildings is changing the face of farming infrastructure.
According to Andrew Telford, owner of Telford Building Systems, the instant asset write off and growing confidence in the Australian agriculture sector has driven increased demand for shedding. �Farmers, on the east coast especially, have come out of drought and are heading for a good season. There�s a sense of renewed confidence.�
Supporting australian manufacturers
Trevor Walker, National Wholesale Manager at Now Buildings, says the company has also seen strong demand and adds that farmers are going back to Australian-made steel for their sheds. �In 2020 we saw a strong swing back to Australian-made sheds. Part of that is that with COVID-19 people see it as important to be supporting Australian industries but there are also more practical reasons.
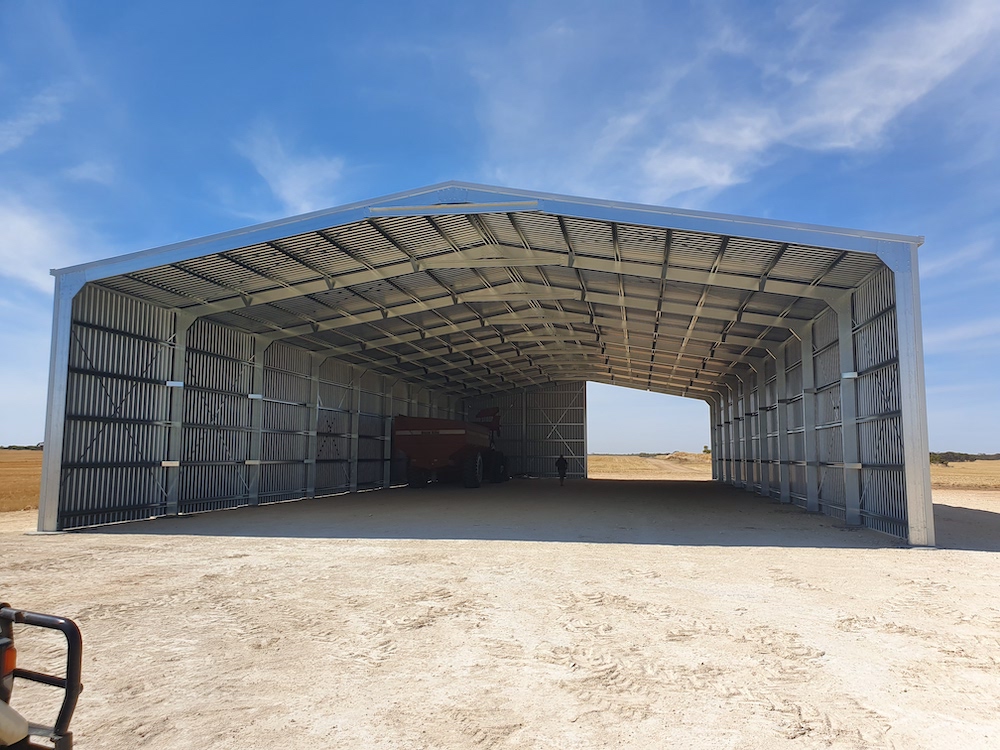
�Delivery of sheds where the steel is sourced from China is getting slower as the lead times keep pushing out but there is also a swing back to Australian made steel because of the quality aspect.
�Some steel that comes from overseas, mainly China, is as low as 100 MPa (megapascals, a unit that measures the stiffness, tensile strength and compressive strength of materials in construction) where we�re supplying steel that�s graded from 450 to 500 MPa. The steel looks similar but there is no comparison in performance.�
Trevor Walker
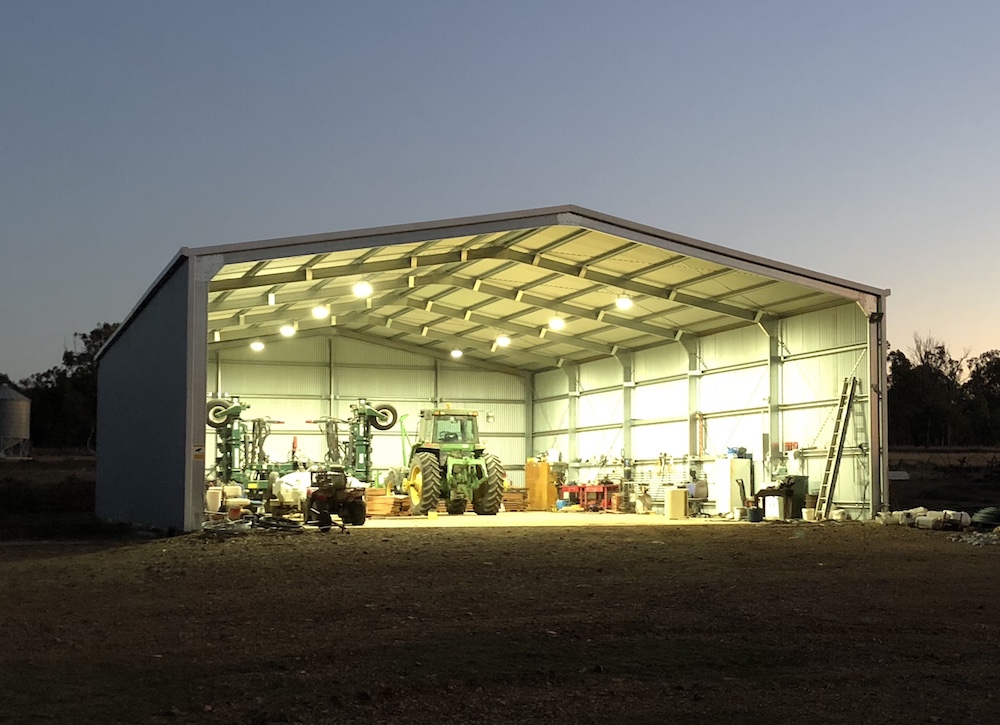
Both Telford and Walker are seeing a trend towards larger sheds. �Sheds are just getting larger,� says Telford. �Machinery sizing is also increasing, so the sheds have to get larger as people are conscious of protecting expensive assets from the elements. Hay sheds are getting bigger and bigger as people seek to reduce their risk in future droughts and shelter for stock in feedlots is getting bigger and bigger as well.�
�We are seeing requirements for larger openings and higher buildings,� says Walker. �And we are opening up the gable ends rather than the long side so there are no posts in the way. Even if the openings are in the long side, machinery has got wider and higher. Thirty years ago, a farm shed would be 3.6 metres high and now they are between 5 and 6 metres high. As a lot of the new machines are too big for the old sheds, especially the opening, farmers are buying new ones.�
Walker and Telford also agreed that while some farmers will buy solely on cost when it comes to purchasing a new shed, in most cases it comes down to more intangible factors such as reputation and a company�s track record. According to Telford, �Time frames are also important. A lot of farmers will hold�
off buying a new shed until they have got the crop off or sold the weaners so it�s important to be able to deliver when they are ready.�
Walker adds that flexibility is also important. �Our business is 90 per cent rural and no one has ever said that shed you built is too big, so our system allows customers to extend their shed in any way, except up. No one buys all their shedding in one go but that flexibility means people can add a lean-to or a couple of bays so if they have a good season, they will order an extension.
Storage boom after bumper harvest
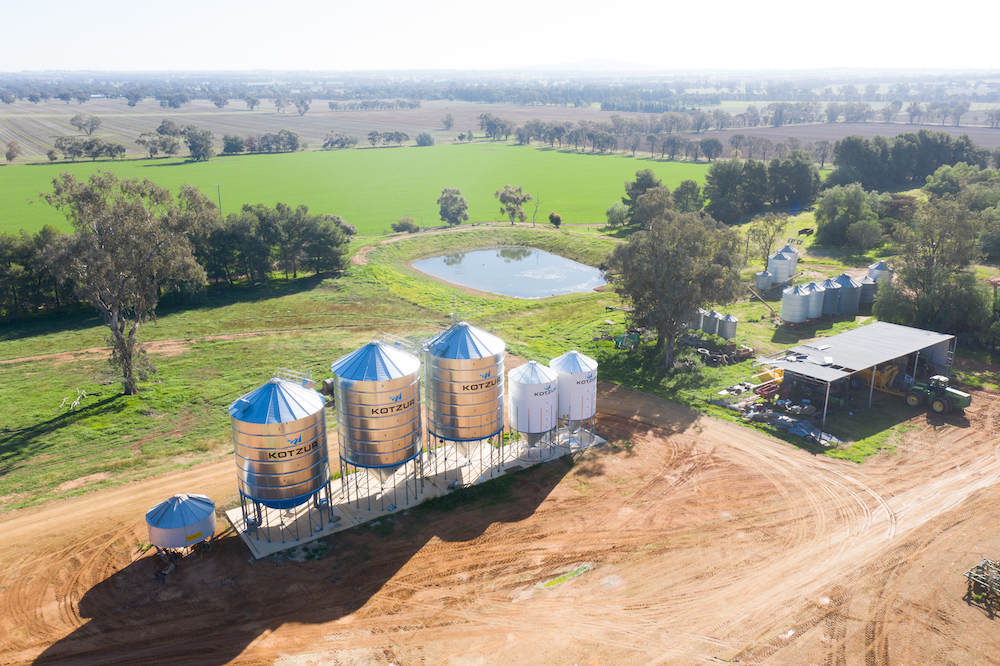
The bumper harvest on the east coast is also driving demand for on-farm grain storage. Kotzur Silos managing director, Andrew Kotzur, says that demand is the strongest it has been since 2015. This year started looking like a wetter harvest so there has been a lot of interest around moisture management, getting the crop into the silo and then cooling it and drying it. We can incorporate aerated storage into silos, basically electric fans driving ambient air, and so demand for that product has been strong.
More generally Kotzur is seeing the trend to on-farm storage of grain continuing to grow. Grain producers are implementing higher capacities of grain handling and there has been a surge in automation in grain handling to improve the logistics of harvest.
�Fixed handling machinery such as augers and drive over road hoppers are becoming more popular,� Kotzur says. �Growers are also looking to be able to blend grain whether it�s to meet quality factors such as protein levels or blending out screening etc.�
Despite grain producers being nervous about the implications of the looming trade war with China, Kotzur says he is not seeing producers looking to increase storage as a result of that uncertainty.
�It�s too early to see the China situation having an impact as a lot of grower made decisions on their storage before that started to become an issue. The $150,000 asset write off measure in the budget is having an effect, however. Grain storage has had favourable tax treatment for a while now, but that measure is a strong influence.�
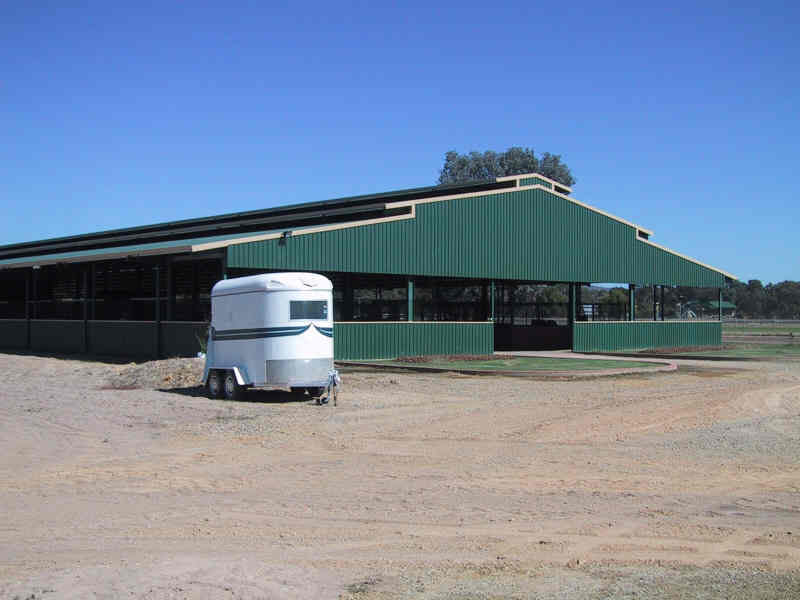
Surge in renewables
Another key trend in farm sheds and infrastructure is that they are increasingly being used to house solar installations. According to both Telford and Walker, reputable shed manufacturers are engineering roof loads in because of the likelihood that solar panels will go on at some point in the shed�s lifetime.�
Upton Engineering managing director, Paul Upton, says pumping costs for stock and irrigation water is a major farm expense and the use of solar can dramatically reduce operation costs when pumping water. As a result, the company is partnering with large solar providers to offer cheap electrical power rates to farmers who have ideal conditions for large scale irrigation pumping and a suitable site for a solar�array.�
�We are seeing a lot of windmill replacement going on and the systems are beginning to increase in size and are being put to use in pumping for irrigation water. Solar arrays can be set up in two different ways, the first is to directly run the electric pump from the solar panels if there is no grid connected electricity on site.
�The second way is to have a large solar array that is grid connected and use the solar input to the grid to offset the farm power bill. An irrigation solar system can easily see a solar panel array of 100kw in size.�
Paul Upton
Red Earth Energy CEO, Charles Walker, is also seeing a lot of interest from irrigators. �With electricity costs rising, we have seen enquiries double. Irrigators especially are farming to the tariff rather than what is best for the crop and they are looking to change that. For farmers who are off-grid, renewables pay back the investment in as little as four years, but the capital costs are still an issue.�
If you enjoyed this feature on post-harvest infrastructure, you might enjoy our story on vertical farming.
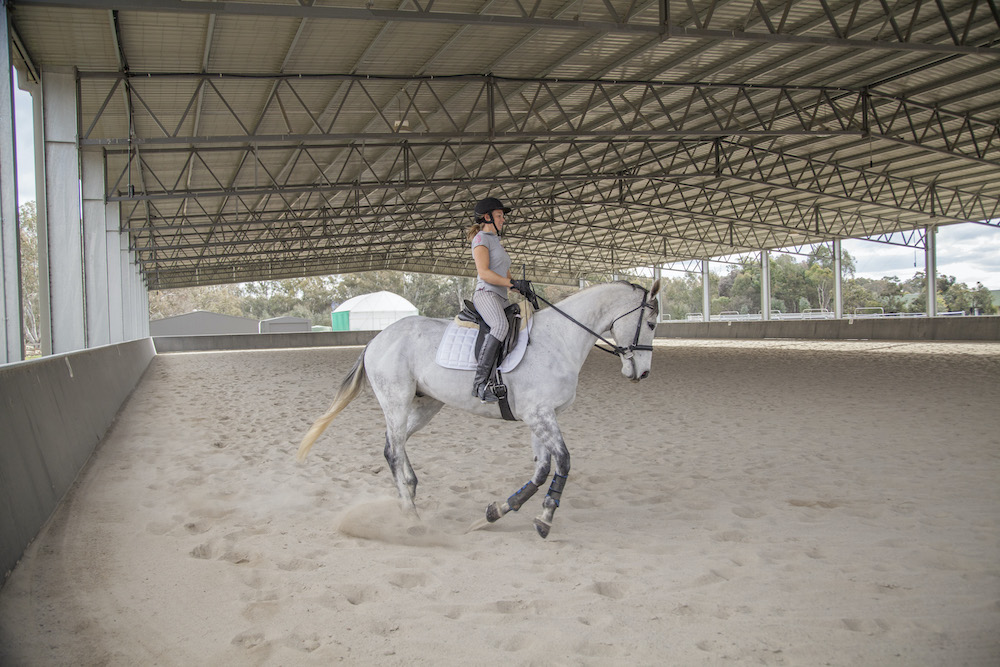